PCBA = Printed Circuit Board Assembly.
PCBA refers to the assembly of PCB into a finished product by SMT mounting, DIP plug-in and testing. We can understand it as a finished PCB.
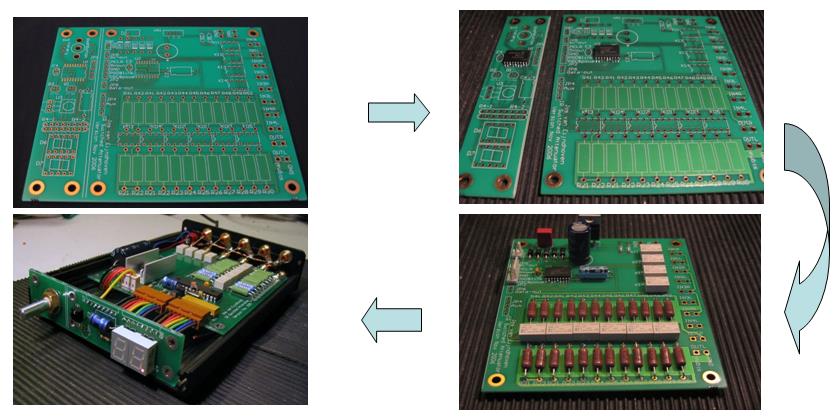
The production and processing process of PCBA is very complex, including the production of PCB, the procurement and testing of electronic components, SMT mounting, DIP plug-in and other processes
PCBA testing is an indispensable and important link to ensure the quality of product delivery. It determines the performance of the product, controls the quality of the product, reduces the after-sales and repair rate, makes customers more trustworthy, and promotes win-win cooperation between enterprises and customers.
PCBA test refers to the test of electrical continuity and input/output values of PCBA circuit boards with electronic components mounted. In the design of PCB circuit board, there is a numerical relationship between different test points, such as voltage and current. It is necessary to use professional test equipment or manually operate a multimeter to test the test points to verify whether the actual PCBA board meets the design requirements. PCBA test is a key step to ensure the quality of production and delivery. The FCT test fixture is made according to the test points, procedures and test steps designed by the customer, and then the PCBA board is placed on the FCT test rack to complete the test.
PCBA test principle
Connect the test points on the PCBA board through the FCT test rack to form a complete path, connect the computer and the burner, and upload the MCU program. The MCU program will capture the user's input actions (such as pressing and holding the switch for 3 seconds), and control the on-off of the side circuit (such as LED flashing) or drive the motor to rotate through calculation. The test of the whole PCBA board is completed by observing the voltage and current values between test points on the FCT test rack and verifying whether these input and output actions are consistent with the design.
PCBA test rack
The processing of large quantities of PCBA boards must be tested. Generally, corresponding test racks will be issued to assist in efficient completion. The principle of the test rack is to connect the test thimble with the test point of the PCB board, obtain the key data such as voltage and current in the circuit when it is powered on, and display them on the display screen of the test rack to achieve the purpose of rapid detection. When customers design PCB boards, engineers will consider their test plans, reserve PCB test points, and issue professional test documents or test plans to manufacturers. We can make PCBA test stand (equipped with engraving machine and test stand assembly engineer) by ourselves.
PCBA test types are as follows:
ICT (In Circuit Test) test: It mainly detects the voltage/current data at the test point after the PCB is powered on, and does not involve the test of function keys or input/output.
FCT (Functional Test) test: First, you need to burn the prepared MCU program into the program IC through a burner (such as ST Link, JTAG), so as to achieve the corresponding functional test. For example, after pressing the key, the LED lights up Press two keys at the same time to restore factory settings, etc. Of course, whether all functional tests can be carried out must be based on the premise that the PCB welding is OK and the circuit is conductive, otherwise it cannot be realized.
Burn In Test: Simulate user input and output for a long time and periodically for PCBA that have been burned and passed FCT to test their durability and welding reliability. Under special circumstances, it is also necessary to expose the PCBA board to a specific temperature and humidity environment.
PCBA testing is an essential and important link in the whole PCBA manufacturing supply chain. Quality is controlled from the final data results. In the standardized design and manufacturing management, PCBA testing must be recommended and implemented.
OPCBA provides customers with high-end SMT patch processing services, and is equipped with 12 full-automatic high-speed SMT patch production lines, full-automatic loading machines, full-automatic solder paste printers, SPI solder paste thickness detectors, multi temperature zone reflow soldering, AOI optical testing equipment, X-ray inspection machines, baking machines, mesh cleaning machines, etc. Support the mounting of 01005 components, 0.3mm Pitch BGA, QFN and other precision electronic components.
Advantages of our SMT chip processing
1. The quality team with more than 20 people effectively controls IQC incoming material inspection, IPQC process patrol inspection, OQA delivery inspection and other important process links
2. A team of 10 electronic engineers is provided to put forward constructive improvement suggestions for DFM manufacturability inspection and engineering process in the production process, effectively improving product quality and production efficiency
3. Promote the Quick Response mechanism. The professional sales staff will connect with customers and respond to any abnormal situation within one hour
4. Promote MES electronic information board, effectively supervise PMC production planning process and ensure delivery date
5. ESD static protection pearl cotton or static bag shall be used for safe packaging to ensure the safety of products during transportation.
How to cooperate with PCB Assembly?
You just need to send the BOM, GERBER and coordinate files of relevant projects to us for quotation. After the price is determined, you can prepare the materials and PCB boards and deliver them to us for verification, and then start the relevant PCBA services.